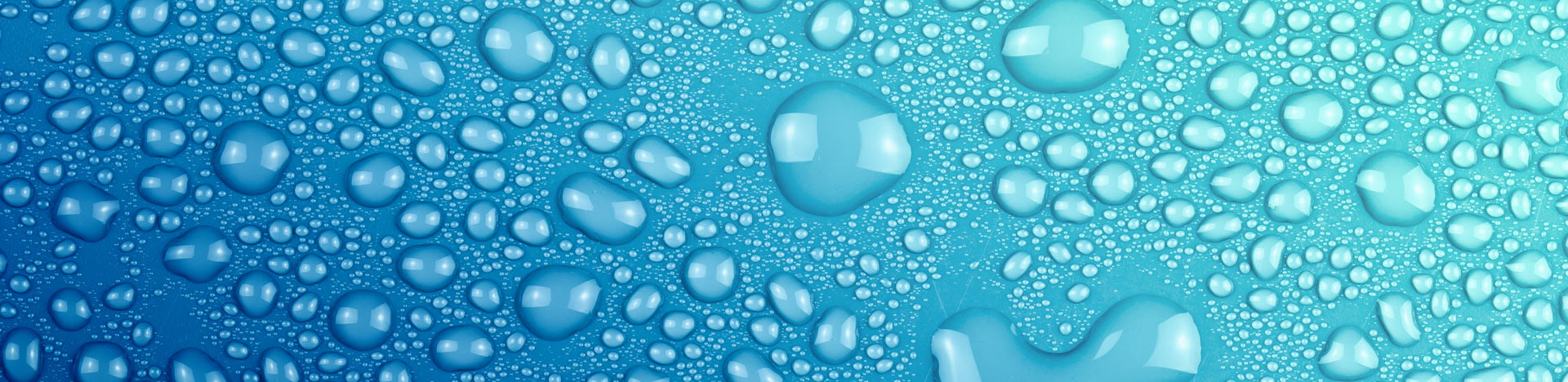
CM-151 UF Membrane helps semiconductor foundry reduce HF wastewater volume to enable reuse and enhance sustainability
CM-151 UF Membrane helps semiconductor foundry reduce HF wastewater volume to enable reuse and enhance sustainability
North American Semiconductor Fab
Download PDFCM-151 UF Membrane helps semiconductor foundry reduce HF wastewater volume to enable reuse and enhance sustainability
Semiconductor fabs and foundries are facing increased scrutiny for their environmental impact, particularly as demand for chip design innovation intensifies. This can put a strain on existing freshwater supplies and potentially jeopardize operations as the industry undergoes rapid expansion to keep up with growing demand for its products.
A leading foundry in North America was experiencing particulate breakthrough in its existing wastewater treatment plant at one of its fabs. The plant relied on clarifiers and lamella settlers, which delivered inconsistent effluent quality. To address this challenge, the fab piloted and subsequently implemented a new approach – to treat HF-containing wastewater from an existing wastewater treatment process via a reuse system that consisted of CM-151 technology and a reverse osmosis (RO) plant.
The streamlined design of the new process (below) included the addition of caustic (NaOH) to neutralize the wastewater stream, followed by suspended solids removal and silt density index (SDI) reduction through the CM-151 membrane system. The CM-151 system’s compact design enabled it to conform to the fab’s space constraints. Further removal of dissolved solids was accomplished through a downstream RO process, which produced water that was of a high enough quality to be reintroduced into the front end of the ultrapure water (UPW) plant. This process design change moved the fluoride removal step to the RO process, eliminating the need for additional costly chemicals (e.g., CaCO3).
The innovative system has proven to be highly reliable, requiring minimal cleaning and oversight. It operates at a 95% recovery rate and has shown no sign of degradation from sustained exposure to the neutralized waste stream. Key operational parameters are captured top right. Implementation of the water reuse solution has helped the facility realize total savings in excess of $800,000 per year. This includes $450,000 in operational savings compared to the previous treatment process, $180,000 in freshwater acquisition and treatment costs, and another $180,000 in cost avoidance through a reduction in discharge fees.