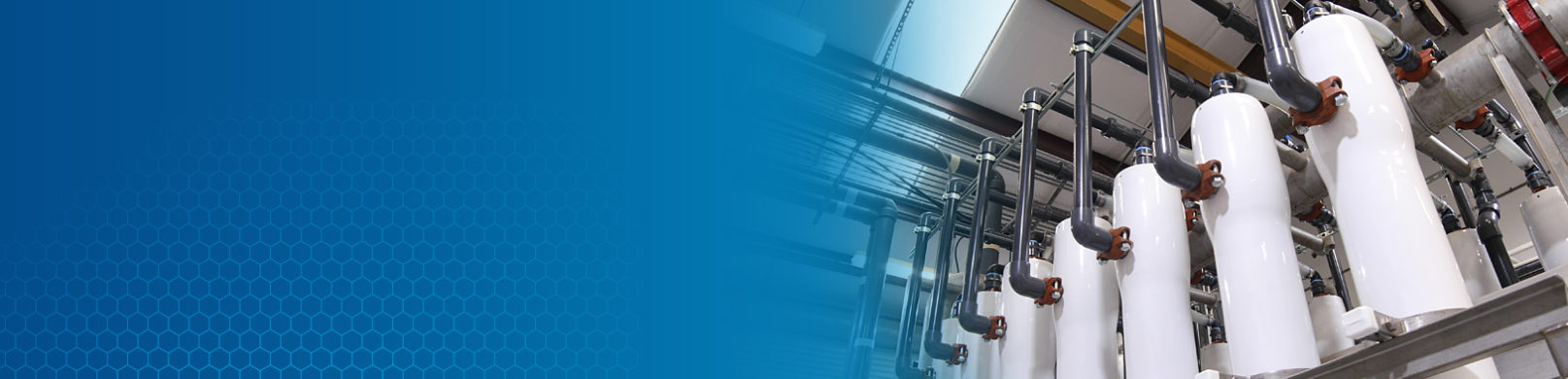
Nanostone Helps Semiconductor Fab Enable Reuse to Reduce HF Wastewater Volume
Reduce operating expenses by $800K

North American Semiconductor Fabricator Enables Reuse of HF Wastewater
A leading foundry in North America was experiencing particulate breakthrough in its existing wastewater treatment plant at one of its fabs. The plant relied on clarifiers and lamella settlers, which delivered inconsistent effluent quality. To address this challenge, the fab needed to:
- Upgrade its existing hydrofluoric acid (HF) wastewater treatment process to address compliance concerns caused by particulate breakthrough.
- A new solution that would enable it to reuse the wastewater, rather than simply meet discharge requirements.
- Realize wastewater reuse and offer additional benefits, including helping the plant meet increased water demand and further reducing its environmental impact.
Nanostone’s CM-151 ceramic ultrafiltration membrane system has proven to be reliable and robust
- By altering the treatment approach, CM-151 not only enabled the wastewater reuse, it also eliminated the need to treat and discharge 100 gallons per minute (gpm) of wastewater.
- The result: more than $800,000 in annual savings through a reduction in wastewater treatment costs, discharge fees, and the acquisition and treatment of freshwater.
- CM-151 is a robust solution that can operate at high flux and treat the HF-containing waste stream reliably within a limited footprint.
- It also ensures more stable reverse osmosis (RO) operation and consistent water quality.
To address this challenge, the fab piloted and subsequently implemented a new approach – to treat HF-containing wastewater from an existing wastewater treatment process via a reuse system that consisted of CM-151 technology and a reverse osmosis (RO) plant.
The innovative system has proven to be highly reliable, requiring minimal cleaning and oversight. It operates at a 95% recovery rate and has shown no sign of degradation from sustained exposure to the neutralized waste stream. Key operational parameters are captured top right.
Implementation of the water reuse solution has helped the facility realize total savings in excess of $800,000 per year. This includes $450,000 in operational savings compared to the previous treatment process, $180,000 in freshwater acquisition and treatment costs, and another $180,000 in cost avoidance through a reduction in discharge fees.